AG&P Ichthys LNG Project – June 2016

AG&P was contracted by JKC to modularize 26 Local Electrical Rooms (LER) and Local Instrumentation Rooms (LIR) that will provide electrical backbone of the Ichthys Project. Ichthys is owned by Inpex and Total, which in turn contracted JKC, a consortium of three global EPC companies: Japan Gas Corporation, Kellog, Brown and Root (KBR), and Chiyoda, to execute their project on their behalf. The entire fabrication and assembly of LER/LIR modules was done in Batangas AG&P yards. Each of LER/LIR modules have HVAC System which provides accurate control of room temperature and air quality. The HVAC Control System uses a redundant Siemens S7-400 PLC system with HMI. The PLC and HMI programs were developed by Siemens U.A.E. But the HVAC Commissioning was done by AEGIS with the help of JKC Commissioning Team. From Loop checking of instruments, Functional Testing of Equipment to Automatic Sequence Test and Cause and Effect Testing of HVAC system for all the 26 LER/LIR modules were the scope during commissioning. There are some program modifications that have been made in order to satisfy the requirements of the approved Control Philosophy. Cyber security was also implemented on all the modules to protect the network, program and data from an attack, damage or unauthorized access. PLC, HMI and network switches are password protected and only the authorized person and computer are allowed to access the program. The HVAC Control System was also integrated to Yokogawa DCS via Modbus communication. Signals such as run/stop feedback, fault/trip status, analog readings and start/stop command were sent from Siemens PLC to Yokogawa DCS. Integrated Factory Acceptance test (IFAT) was done by Yokogawa together with AEGIS to ensure that the Modbus communication is functional.
Holcim Lugait Kiln, Cooler & Coal Mill Upgrade from S5 – May 2016
After successful efforts in upgrading several plant sections from S5 to PCS7 platform, Holcim Lugait approached the final phase of the control system upgrade. Just this recent May 2016, the most critical and complicated process sections of a Cement plant (Kiln, Cooler and Coal Mill) was finally upgraded to PCS7 Cemat. The upgrade was dedicated for the annual SPS schedule in Holcim Lugait Plant shutdown which ran for almost a month. A number of third-party equipment were integrated during this upgrade. There was the simplification of two cooler fans into one larger drive cooler fan using ABB drives FPBA, the implementation of Sinamics drives for the Cooler EP fan, the use of Profimess power monitoring and the application of Siemens Robicon for RSP fan. All these solutions were integrated to the system via Profibus Communication to facilitate necessary motor control, process monitoring and real-time status updates. Also, Siemens diagnostic repeater was used first-hand in this upgrade. Its diagnostics and functionality helped in troubleshooting certain problems in the network communication efficiently. The Plant Automation team, also, used Profitrace in testing the signal consistency all throughout the bus line to re-assure that there will be no another plant shutdown cause of communication failure. A typical redundant optical ring topology was implemented to link several Remote IOs from different MCC rooms.The whole conversion of the S5 program to PCS7 Cemat standard and the reconstruction of screens for the WinCC SCADA was solely accomplished by system Integrator Company, KMI lead by Sir Martin Messer. Aegis supported the plant in every automation activities inside and outside the Control Room. From testing communications between fibers, checking profibus terminations and even in simulating the program up to commissioning until plant normalization.
Holcim La Union PCS Upgrade from ABB System – March 2016
The deteriorating performance of the old ABB Control system with component spare parts getting obsolete and lacking of local support triggered Holcim La Union to upgrade their Plant’s Control System. Started early January of 2015, La union adapted and upgraded the control systems under Siemens’ PCS7 solution using state-of-the-art PLCs and other automation components increasing the Plant’s process efficiency and reliability. Following Holcim’s plant standardization, Process Control System used PLC S7-400 with all necessary hardware such as ET200 IO modules, Switches/Scalances, Industrial Rack PCs, etc., and related software for motors and process controls. Like the past approach of ABB, Siemens’ PCS solution was interfaced with standard Holcim products for High Level Automation and Technical Information System (TIS). AEGIS Team being the Main Contractor for the upgrade followed the Holcim Asset Code (HAC), Holcim Platform Architecture Guide (PAG) in converting the program into PCS7 CEMAT standard and creating new screens for process monitoring and controlling. With that being implemented, AEGIS programmers adapted Holcim software library and applied programming procedures including standards on HMI screen design and documentation. Also, the concerned system integrators applied standard network configuration and communication using Profibus DP for PLC to I/O connection and Ethernet protocol for PLC to PC servers and Operator stations communication. The said Plant-wide Upgrade involved all the sections of the cement operations except the crushing site. AEGIS programmers worked on re-creating the programs for at least 5-month long duration concerning all motor control, PID controllers, Analog supervision, Valves, Dampers and all related instruments. AEGIS team were requested on-site a month before the plant shutdown in preparation for the commissioning. During that duration, all the installation and configuration of all PC stations for servers, engineering and operators were done straightforwardly. Third-party systems and equipment like Schenk Weigh feeders, ABB drives and DALOG were integrated to the PCS 7 system Also, all the sequence and necessary interlocking were carefully reviewed and confirmed during program simulation with the supervision of Plant’s Automation Head, Engr. Glenn Piza. In relation to the upgrade, AEGIS Team needed to conduct necessary hands-on training for operators to adapt themselves on the new interface of PCS 7 CEMAT System. Through the knowledge and support of La Union’s Engineers and Technicians, the testing and commissioning was done efficiently decreasing any chance of delay of the start-up. At the final phase of the project, the days for normalization were extended for the fine tuning and for the operators to have enough time to adapt themselves with the Control System.
Eagle Cement Line 2 Automation Minerals Standard – February 2016
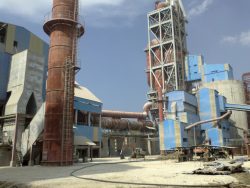
Eagle Cement Corporation awarded Siemens PH with the Automation for their Cement Plant Line 2. In line with this, Siemens trusted the engineering services to their solution partner AEGIS being known as a specialist for cement industries for the past years. The project was spearheaded by Mr. Cesar Bendoy of Projects Department with the help of Mr. Jun Gutierrez from Automation/Instrumentation. Advanced planning was the key of the project for a more convenient execution until the end. ECC supplied the needed documents for the Crusher, Rawmill, Coalmill, Kiln & Cooler. For this line, Cemat Minerals Standard was used for the programming which was really appreciated by the technical and production for its features that simplified their troubleshooting and operations respectively. They first commissioned the Rawmill area which are integrated to HEFEI for the Rollerpress and HASLER for the weighfeeders. HEFEI Rollerpress was communicated via profinet and HASLER weighfeeders was communicated via profibus. The Rawmill commissioning was finished with an orderly manner. The Kiln and Coalmill area were simultaneously commissioned. All of the PA instruments were directly configured in PCS7 and can be monitored for Kiln and other areas as well. The Coalmill equipment was supplied by a third party supplier and the controls were programmed in the Line 2 PCS7 Cemat Server-Client network.
Lafarge Bulacan Finishmill 5 Upgrade from S5 – January 2015
Cement Giant in the Philippines LaFarge RCC upgraded one of the sophisticated Cement grinding system, HOROMILL, in one of its cement plant in Bo. Minuyan, Norzagaray Bulacan early January of 2015. The system improvement was facilitated by Fives FCB’s Automation French Engineer, Engr. E. Trouto assisted by some of AEGIS Inc. Systems Engineers and was supervised by plant’s Automation manager Engr. Ronald Simbulan. The upgrade was limited only on the software portion of the system as the hardware component were already been upgraded. The grinding system was integrated to the existing PCS Control System of the said Cement Plant using Siemens’ Simatic Communication Processor via Profibus DP to the remote field instrument IOs and necessary PCS7 Software and Licenses. Certain alterations from the original S5 program were carried out to enhance the Mill’s operation and increase system efficiency. Also, improved start-up and stop procedures of Horomill were applied prior to the new functional analysis made by FFCB. These modification increased the cement productivity of Lafarge RCC Plant. The system upgrade was done successfully in a span of one month including normalization and fine tuning of controller parameters.
Holcim Lugait Rawmill and Crusher Upgrade from S5 – October 2014
After the positive feedback from Holcim Bulacan’s upgrades, another upgrade project was trusted to AEGIS. Holcim Lugait’s Rawmill and Crusher area was needed to be upgraded from its existing S5 Controller and COROS LS SCADA to PCS7 Cemat Holcim Standard with the S7-400 controller. All programs were analysed and confirmed thru the new symbol list and IO system. The existing remote S5 controller of the Loesche VRM was already removed and its program was already integrated to the new CPU but this time it is represented thru Cemat Holcim Standard. KMI, was also there to confirm all the programs that were converted and make sure that the process flow was correct. Existing VFDs and power meters were also integrated to the PCS7 system thus, providing comprehensive monitoring and control for the said field devices. After the testing and commissioning of all equipments, with the help of Holcim’s PCS Team, the startup was commenced. The Rawmill area was the first to be started since the Kiln was ready at that time. The crusher was then tested, and AEGIS supported the plant up to normalization. Minor changes were done at the end but as a whole, the plant is back up and running. Thanks to the teams of Holcim PCS, KMI and AEGIS for making the upgrade systematic and free of reservations.
Cemex Cebu 3k Silo Upgrade – June 2014
June 2014 marked the completion of 3K silo extraction project in Tina-an Naga City, Cebu. The project was closed through the combined efforts of EESi and AEGIS in coordination with Cemex Electrical and Automation Team. EESi covered the supply of new field instruments for the 3k silo extraction as well as the additional Allen Bradley IO components and Siemens ET200M IOs for the integration of the said extraction to the existing packing system of the Plant. Supply of new PLC panel, MCC cabinets and related electrical works were also part of their scope. On the other hand, AEGIS supported on the Automation related works (Programming, testing, FAT of Panel and Commissioning) for Silo Extraction Area. The Programming focused on the additional motors and field instruments needed for the automatic control of silo extraction which were integrated to the Plant’s existing packing Server-Client System under Siemens Step 7 and WinCC commissioned by GRAM industrial around year 2011. As per advised, the same standard used in programming of Packhouse area were applied for the programming of the new Cement Silo extraction system. Network communication via profibus was configured and tested smoothly. The new system for silo extraction started its operation 3-days after the actual target of start-up due to some delay in civil related works on the Cement Silo.
Lafarge Bulacan Packhouse Upgrade from S5 – May 2014
After the successful migration from S5 to S7 of the Rawmill area, next in line was the Packhouse area. Initially, the control of the Packhouse, including the S5 controller and Coros SCADA, was located locally near the process area. Fiber-optic cables were laid out from the Central Control Room to the Packhouse area to enable remote control of the process. The S5 Controller was replaced by a S7-400 controller and the program was merged with the existing Finishmill server. The shutdown period given was just 4 days since the plant cannot allow the stop of production for packhouse for a very long time. With the amount of time given, AEGIS was able to do the testing of the equipments and groups before the start-up phase. Production resumed the process, but this time the control was already from the CCR. With the Packhouse upgrade, seamless and efficient migration was done even with a limited time, and that’s AEGIS workmanship.
Lafarge Bulacan Rawmill Upgrade from S5 – March 2014
Lafarge Bulacan has an existing Simatic S5 controller and COROS LSB software for their SCADA while utilizing a CEMAT Standard v3 as its library. Their Preheater, Kiln, Cooler and Coalmill was first upgraded using PCS7 v6 with CEMAT Normal Standard. This time, the Rawmill area was the next to be upgraded by replacing the S5 Controller with S7-400 Controller and its program was added to the existing PCS7 multiproject of the pyroprocess while retaining its IO modules in the field. With familiarity with S5 Programming and Cemat Standard, AEGIS team were able to analyse and convert the S5 Cemat Program to PCS7 CFC while using the Cemat Normal Standard as the plant required. Proper program FAT was done with the help of Lafarge engineers and operators by confirming the process flow with the use of the program simulation. Testing of individual equipments and groups were done to assure proper operation during startup. As the kiln was already started after preventive maintenance shutdown, the startup of rawmill groups was commenced. All of the groups from transport to mill feeding was able to run with proper sequence and interlocking as expected during program FAT.
Holcim Lugait Finish Mill 2 and 3 Upgrade from S5 – October 2013
Like any another manufacturing plants concerning their control system, Vendor’s Support and Spare parts are being obsolete causing expensive maintenance, old systems being incompatible with new products, decreasing speed, limiting storage, declining reliability and efficiency causing unplanned shutdowns initiated Holcim Lugait Plant to face the issue of upgrading their control system. Early October 2013 Lugait Plant took a leap in upgrading their control systems starting with their two cement grinding areas (Finishmill 2 and 3) from S5 platform to PCS7 Cemat Standard using S7-400 PLC. The first initiative to upgrade the system was carefully planned and designed by the whole Holcim PCS Team headed by Sir Michael Gumba in coordination with Holcim Lugait’s Automation Engineers and Technicians supervised by Sir Jejay Limpangog and Sir Rudy Tan. With this project, the backbone of the new Control system was created which is essential for upcoming upgrades of other process sections. Siemens role in the said project was to supply necessary automation components such as IO modules, s7-400 PLCs, Simatic Rack PCs for Redundant Servers, Engineering Station and Operator Stations for process monitoring and control. Hardware installation and configuration as well as establishing the network communications between PLCs and Computer stations were also part of the third-party automation scope. A ring fiber optic communication and profibus communication were the protocols used to establish connections between automation components. The attempt to convert the S5 program into PCS7 Cemat standard blocks and recreating the HMI/SCADA was handled by Lugait’s trusted third-party Programmer, Martin Messer of KMI Germany and two of Aegis Team Engineers, Alwyn Chua and Dennis Racelis. After program adaptaion to the upgraded system it was thoroughly reviewed and simulated with Plant’s Process engineers and Central Control Room (CCR) operators. With this, the testing and commissioning was done efficiently minimizing any chances of delay of start-up. During normalization sudden stoppages were experienced because of profibus communication failure. This was immediately resolved by limiting the communication baud rate/speed up to 500mbps and checking if profibus cable lay out were near to any power lines. Unfortunate troubles like this can now be projected as we charged it to our experience. Lastly, the days for normalization were extended for the operators to have enough time to adapt themselves with the new Control and Monitoring interface with the new Control System.
Eagle Cement Finishmill 2 Automation – October 2013
After some years when Eagle Cement’s Line 1 was operational, they decided to build another Finishmill beside their existing Finishmill 1. With almost identical process flow, AEGIS and the Automation team of ECC was able to execute the testing and commissioning of Finishmill 2 with less challenges. This time, the FM2 project was added to the existing PCS7 multiproject of Line 1 and adding an mulit-monitor operator client for monitoring and control of the whole Finishmill 2 area. The Automation team of ECC was able to contribute more during the testing since they already have a good knowledge of PCS7 and Cemat Standard from Line 1. Commissioning and start-up was just swift and they were able to operate the area within some weeks after the termination works was done outside. A success project not only for AEGIS but for the ECC Team as well.
Holcim Bulacan Kiln, Cooler and Coal Plant Upgrade from ABB System – October 2013
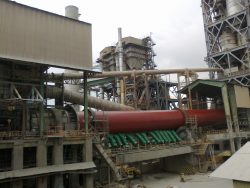
Holcim Bulacan’s Kiln, Cooler and Coal plant was upgraded to Siemens PCS7 from its existing ABB control. The upgrade was done with Holcim PCS team and AEGIS team. New PLC and IO panels were supplied using ET200 modules to cover all of the IO points from the existing control. Since the program was simulated and tested based on the process flow, commissioning and startup was done smoothly and required just ample days for normalization. They also replaced the Kiln main drive with Siemens Robicon which was integrated via profibus to provide basic control and relevant motor status for the operator. Other third-party solutions like Schenk flow meters were also integrated to the PCS7 system which made monitoring and control very convenient for the production.
Lafarge Teresa Finish Mill A& B Automation – September 2013
Another success project for AEGIS as they finish Finishmill A & B upgrade for Lafarge Teresa. For this project, they used their own proprietary motor, valve and group blocks for Simatic STEP7 and faceplates for WinCC to optimize the function of Simatic S7-300 controller. The functions and philosophy of operation was based on Lafarge Cemat Standard with reference from the process team of Lafarge Teresa. Working with the team of Lafarge Teresa and AEGIS engineers, the upgrade was seamlessly done with proper documentation.
Lafarge Batangas Coal Plant Upgrade from S5– September 2013
A successful automation upgrade for Lafarge Batangas was done by AEGIS Inc. as one of their first projects. It was the Coal Plant area of Lafarge Batangas plant that was upgraded from Simatic S5 controller to the latest S7-400 Module with PCS7 CEMAT. The plant is located at Taysan, Batangas. AEGIS Inc. provided the plant with the new motor list including the Coal Crusher Area to give provision for future integration to the system. The scope of the project was from S5 program migration to S7 PCS7 Cemat Lafarge Standard. Included in the project were supply and installation of new S7-400, remote IOs, panel assembly and field termination, operator stations and new profibus layout with conduiting. AEGIS worked hand in hand with Batangas plant personnel during the commissioning, testing up to start-up phase. Documentation was also provided during the latter part of the project for future reference of the cement plant.